IN VARIOUS AREAS
innovation
Over the years, the shipyard team developed many smart solutions, several of which became industry-trendsetters. Research and development re-shaped industry practices and has always been the backbone of the Royal Huisman’s success.
One example is the pioneering use of aluminum for yachts and race boats in the 1960s, 70s and 80s. Another is Project 384, Ethereal, the world’s first hybrid superyacht and launched by Royal Huisman in 2008.

Sustainability
Smart energy concepts and sustainable materials used on new and existing yachts, in order to minimize their impact on the environment and climate. Currently, fuels of the future and various sustainable materials are being researched.
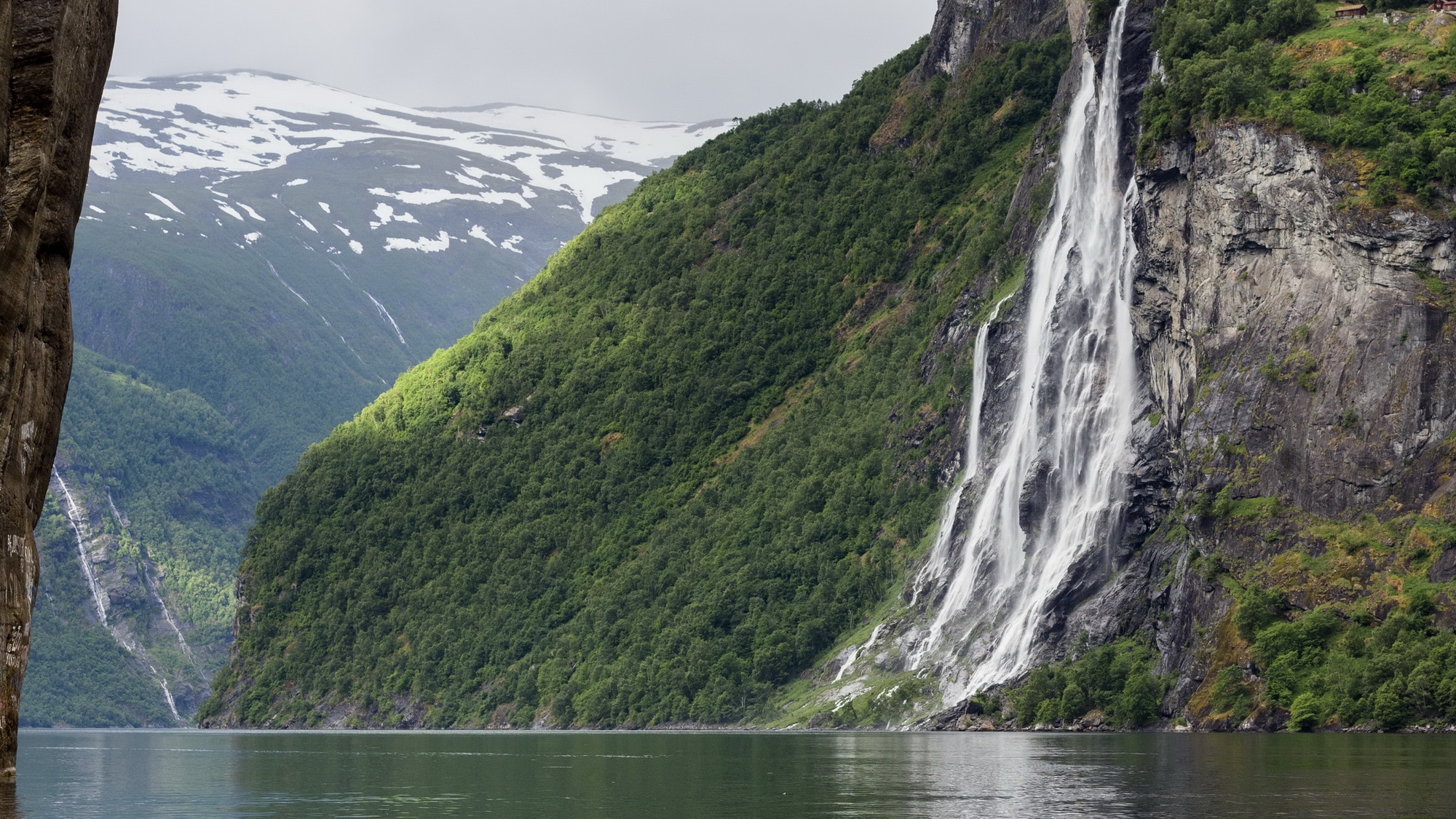
User experience
Focusing specifically on yacht owners and their enjoyment of commissioning and sailing a Royal Huisman yacht, innovative thinking is applied to user experience.
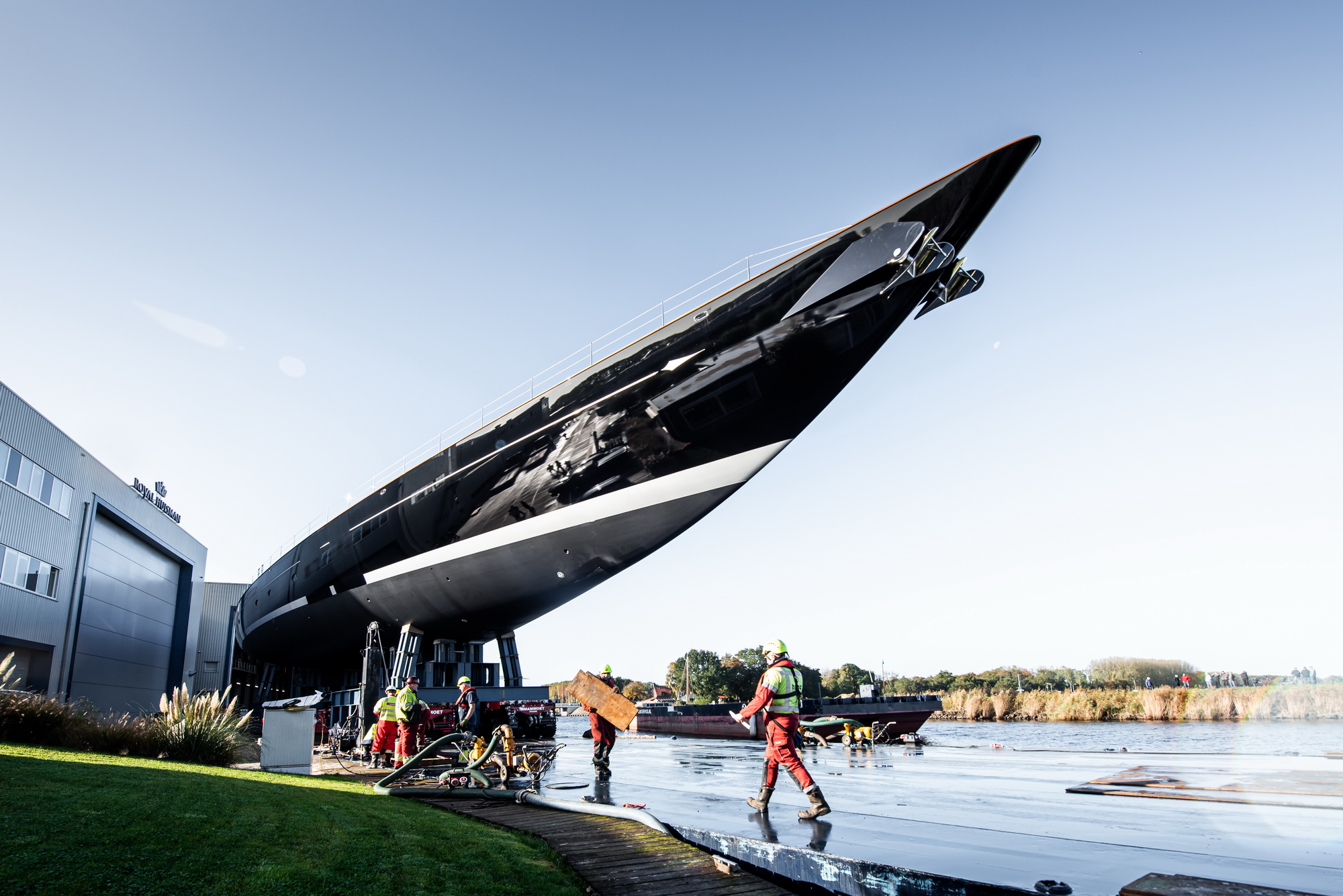
Tools & methods
The latest technology in our design & manufacturing process to improve lead time and efficiency.
.jpg)